an automated factory storage model two independent stacker cranes and a central server system.
This is an automated factory storage model with 15 total storage spaces, where boxes can be loaded / unloaded and controlled by a computer in real-time.
It has total six EV3s: the two EV3s on the conveyer belts run stock LME software and are programmed in LME, while the two cranes and the input conveyer run leJOS.
I connected a leJOS-running EV3 to the computer using a USB cable, using it as the access point to connect with the three other EV3s using PAN.
The AutoFactory model in Command Mode. Note the real-time box storage tracker on the MacBook screen.
The project used socket communication for the computer to send the cranes orders; the video above is running random mode, and other modes include command mode (where you type orders on your PC to control the system) and a text-reading mode so that you can use external loading / unloading algorithms for experimenting with optimization problems. Each of the sockets are connected to the socket server on the PC on separate threads.
We developed this for a premiere Korean engineering college where they will be experimenting with supervised learning methods to create efficient loading / unloading algorithms, as well as showcasing the company's (HandsON Technology) capabilities in developing highly sophisticated LEGO EV3 machines.

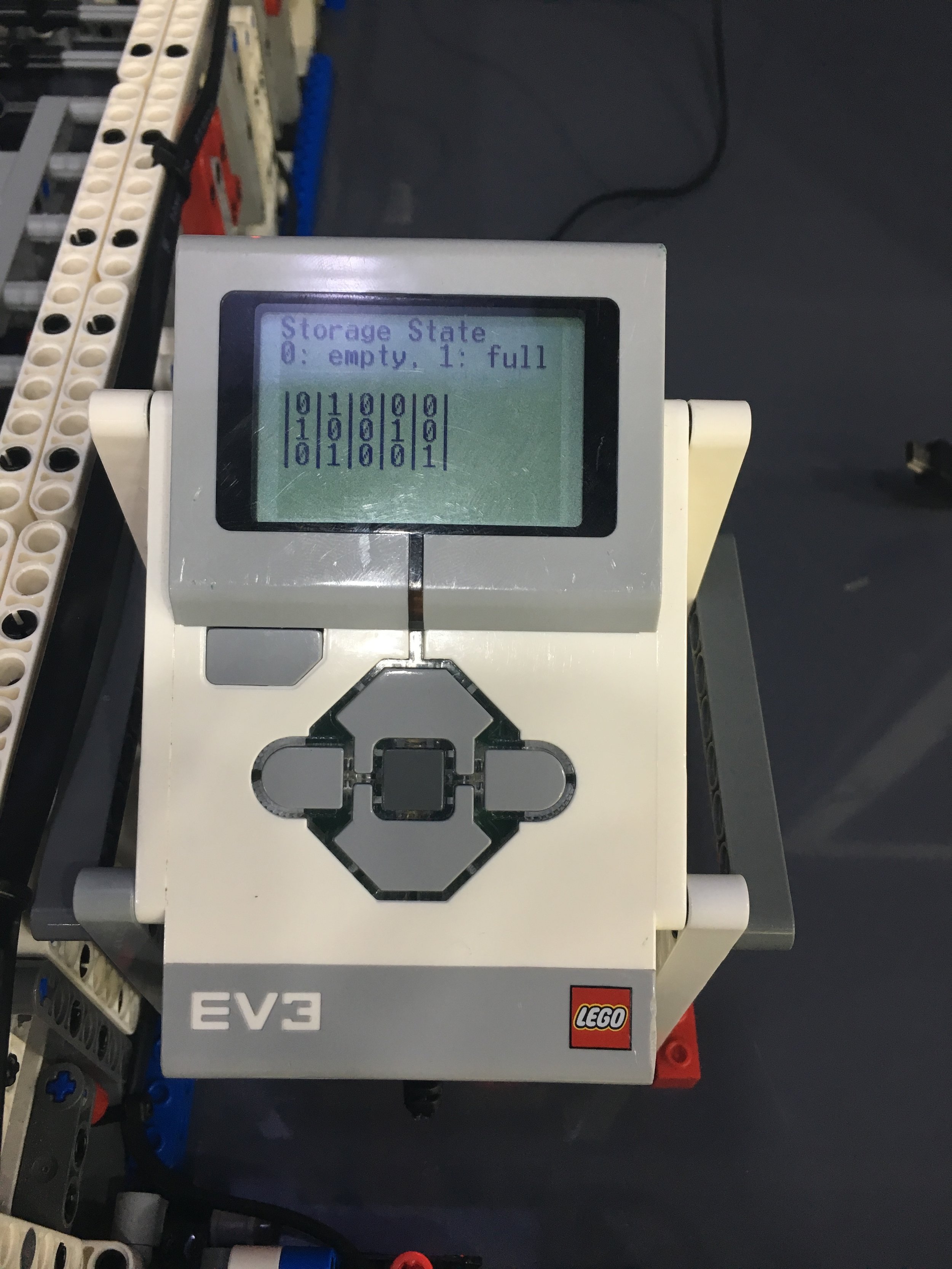
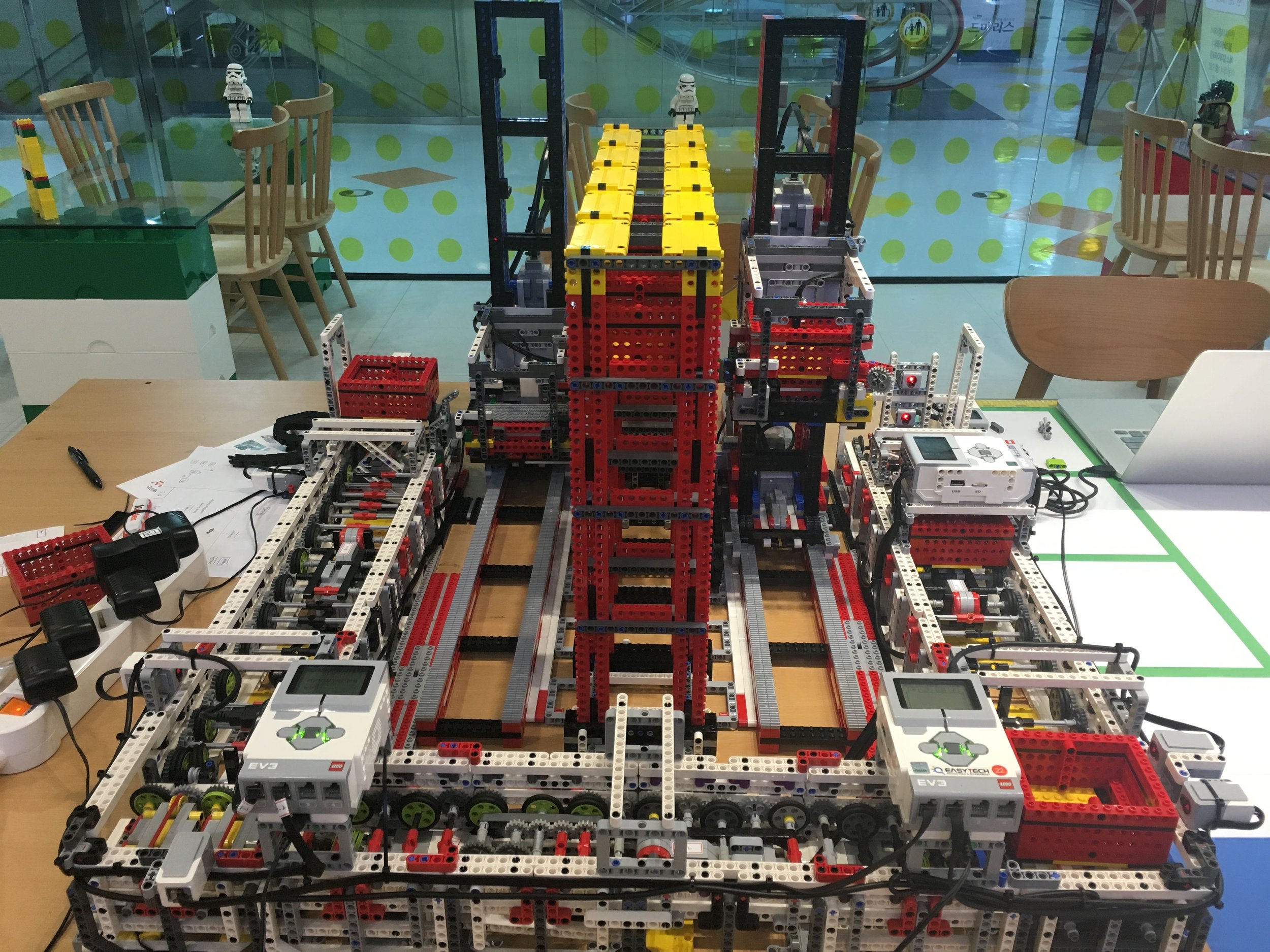
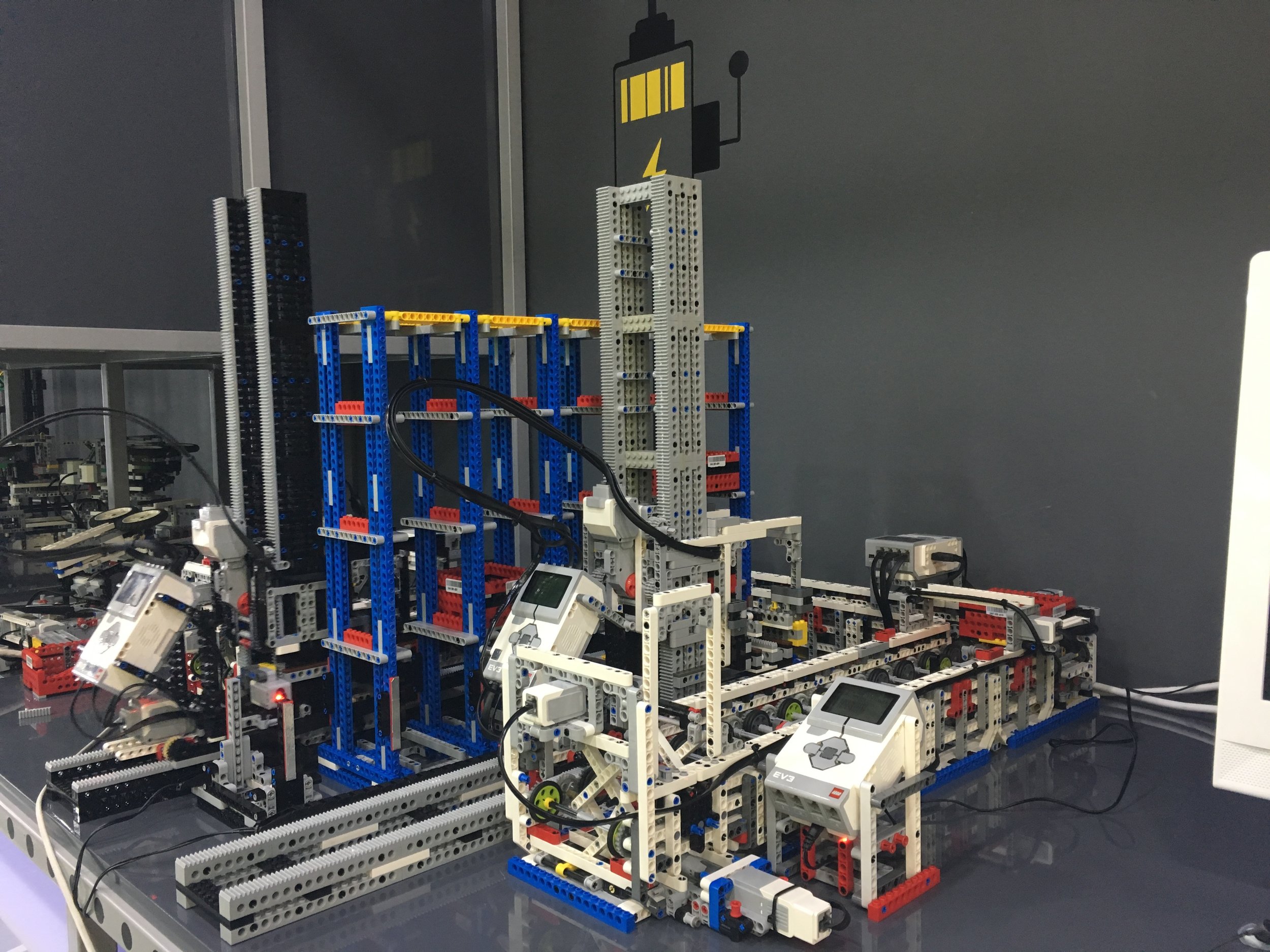
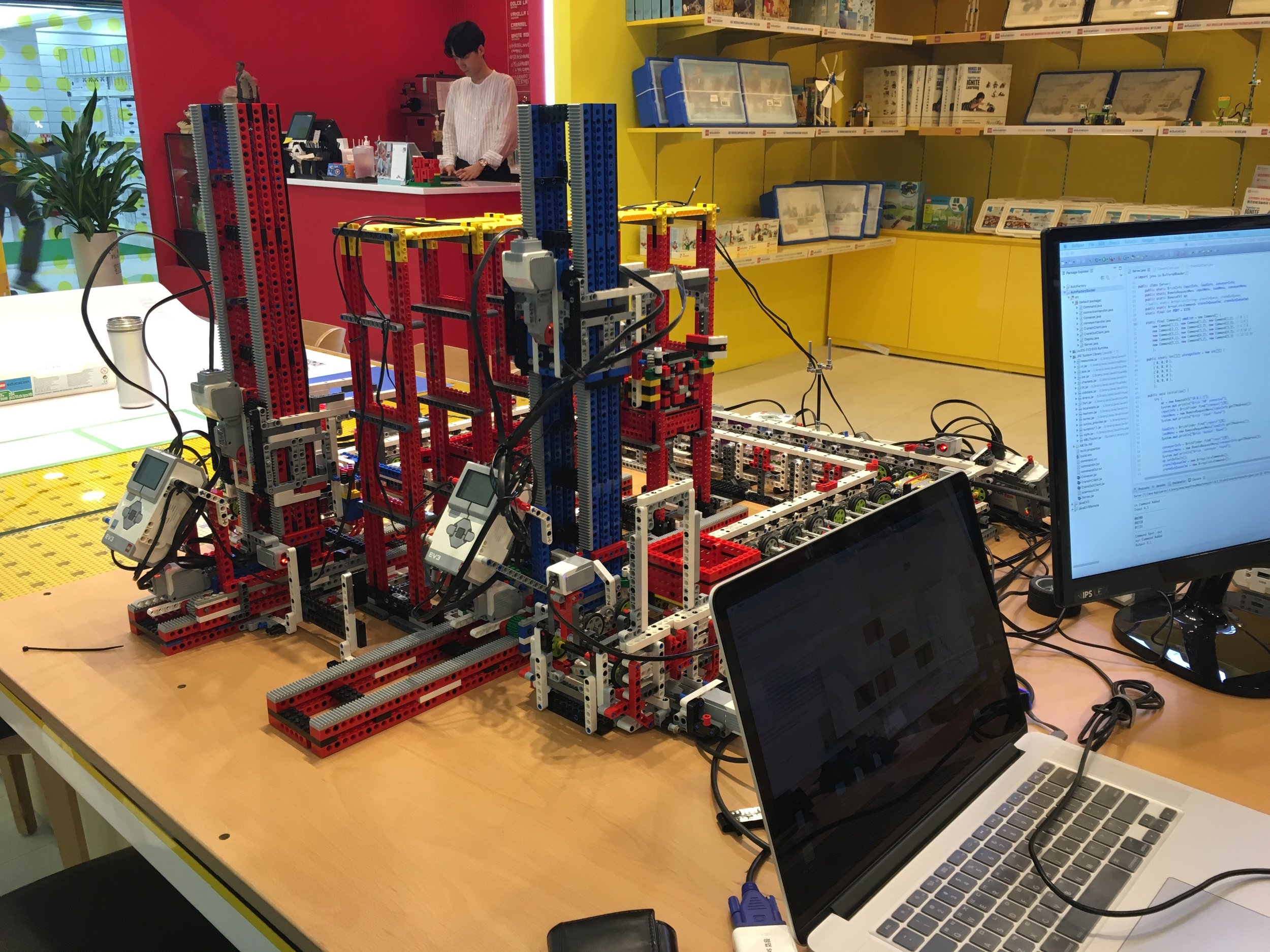